Pre-Filtration: This initial stage removes large particles and contaminants from the crude oil or natural gas stream using coarse filters or strainers. This step prevents damage to downstream equipment and maintains filtration efficiency.
Primary Filtration: Following pre-filtration, this stage targets smaller particles using filters such as cartridge or bag filters. The goal is to achieve finer filtration and improve the quality of the oil and gas.
Secondary Filtration: This stage further refines the filtration process by removing even smaller contaminants, often employing advanced filtration systems like coalescers or centrifugal separators. This ensures the removal of micron-sized particles and contaminants.
Tertiary Filtration: The final filtration stage focuses on eliminating the finest impurities to meet stringent industry standards. High-efficiency filters or membrane filtration systems are commonly used at this stage to ensure optimal purity levels.
The oil and gas supply chain is broadly categorized into three stages, which reflect the company's position in the process. The closer a company operates to the end-user, the further downstream it lies, and vice versa.
The heating oil, often referred to as fuel oil, is primarily used to generate heat or power in engines. Typically derived from crude oil, fuel oils include aviation turbine fuel (ATF), petroleum, diesel, and kerosene, which are widely utilized in various sectors. Additionally, motor oils serve as lubricating purposes in engines and machinery. Before oil can be used in automobiles or machinery, it must be refined to prevent potential harm to engines.
FILTRATION EQUIPMENT AND PROCESSES
Industries employ a range of filtration equipment tailored to specific oil types, such as filter housings, oil filtration systems, industrial filter bags, oil adsorbing bags, oil absorbing filters, and oil absorbents.
During the refining process, oil undergoes purification after extraction to remove impurities. Once refined, the oil is transported, distributed, and prepared for sale, ensuring it meets the requirements of its intended application.
There are various oil and gas filtration systems used globally. Below are some of the most common types you should be familiar with, each designed to meet specific industry needs and improve operational efficiency.
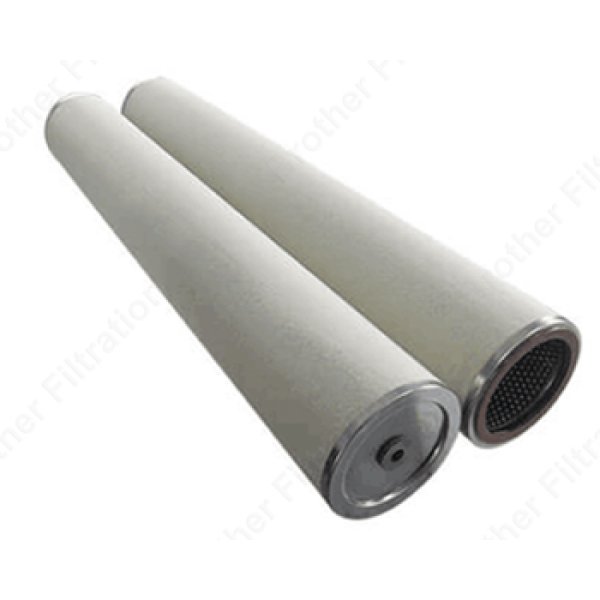
COALESCER FILTER CARTRIDGES
Coalescer filters work on the principle of coalescence, which involves the merging of smaller particles or droplets into larger ones. These filters can separate different types of emulsions and mixtures, particularly for separating water from oil, gas, or fuel.
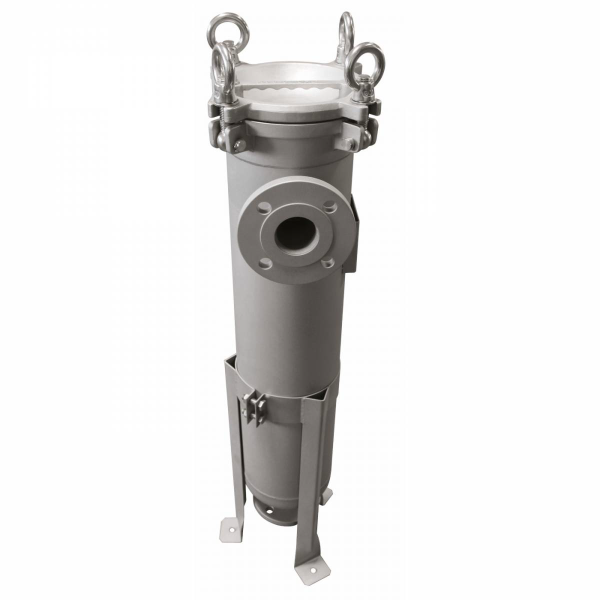
SINGLE BAG FILTER HOUSINGS
Single bag filters, also known as single bag basket housings, are designed for applications with lower flow rates. These filters effectively remove solid contaminants. These filters use a single large bag to capture contaminants, making them cost-effective and easy to maintain.
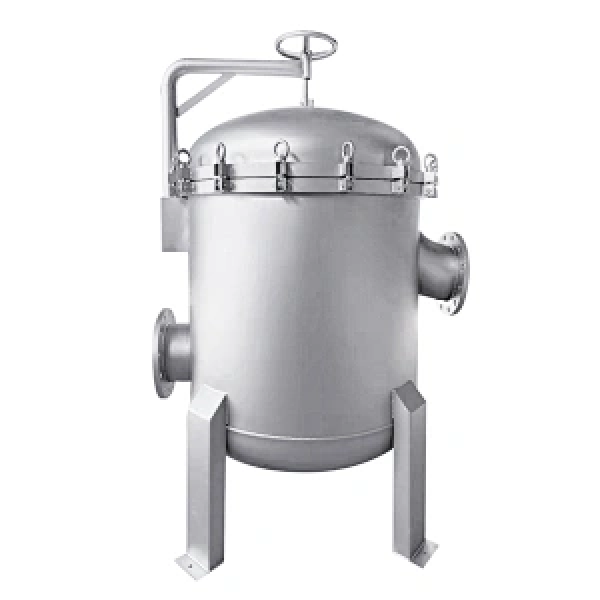
MULTI BAG FILTER HOUSINGS
Multi bag filter housings are designed for higher flow rates and multiple contaminants. These filters typically use between 2 to 12 filter bags, allowing for greater filtration capacity and fewer maintenance interruptions.
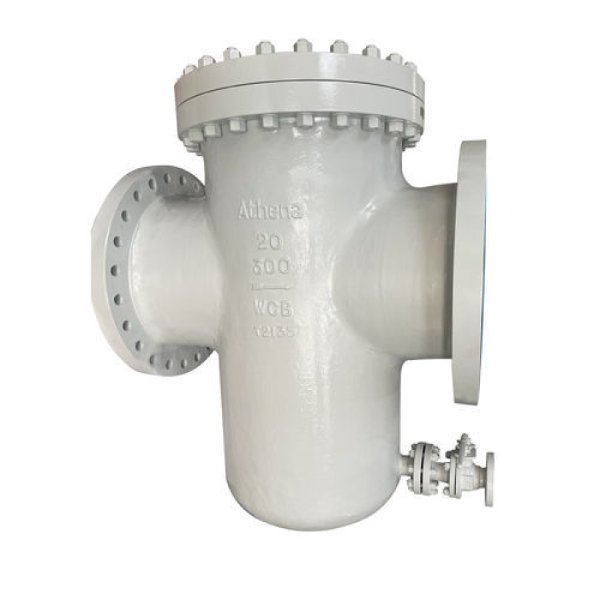
STRAINERS
Strainers are used to remove large particles or debris from the fluid. They come in different types such as Y-strainers and basket strainers, and are often used as pre-filters before more fine filtration processes.
Here are some common filtration applications in the oil and gas industry:
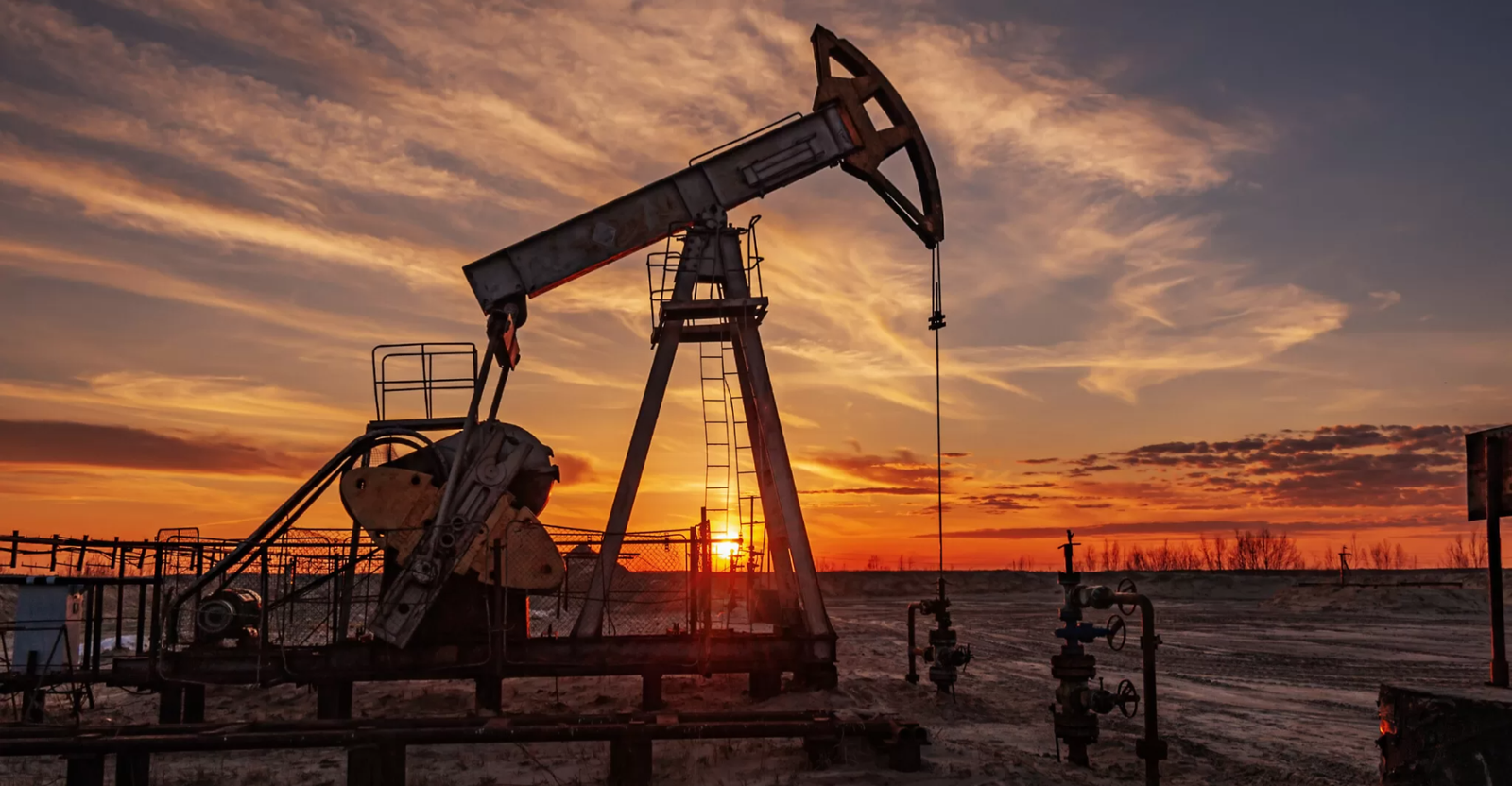
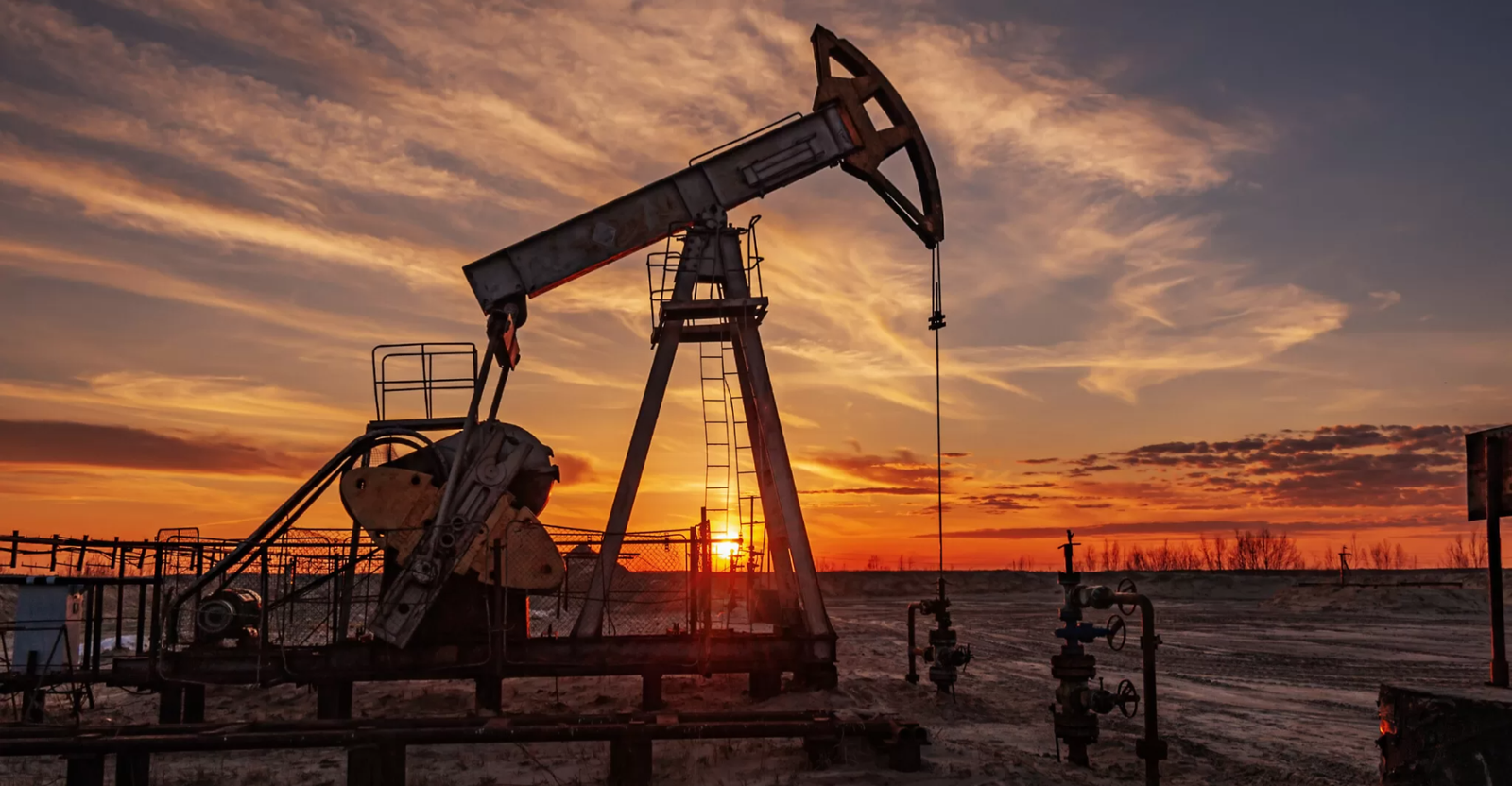